Testing Methods for Safety Glasses Frames and Lenses
Every protective eyewear is designed to shield the wearer’s eyes from various hazards that may occur in the workplace. Therefore, each product must undergo rigorous testing to ensure it functions appropriately. Only glasses labeled correctly can be used as protective eyewear, as this guarantees complete protection against potential impacts.
How Are Protective Glasses Tested?
1. Mechanical Strength
The mechanical strength test determines whether a protective glass receives an “S,” “F,” or “B” classification. During the test, the glasses are subjected to impacts at various speeds:
S: Low energy impact
F: Medium energy impact
B: High energy impact
Since mechanical strength is assessed on both the lens and the frame, if they have different strength levels, the entire protective eyewear receives the lower classification.
2. Corrosion Resistance of the Frames
To ensure the frame withstands extreme environmental conditions, its corrosion resistance is tested. The frame is immersed in boiling sodium chloride solution for 15 minutes, then placed in room temperature sodium chloride solution for another 15 minutes. After rinsing and drying, the frame passes the test if all metal parts remain smooth and corrosion-free.
3. Protection Against Dust and Small Particles
It’s essential for protective eyewear to guard against injuries caused by small particles. This is evaluated using the sand trickle test, where a specified amount of natural quartz sand of defined grain size is poured onto the lens from a height of 170 cm through a drop tube. Subsequently, an optical scattered light test assesses the lens’s condition.
4. UV Protection, Scattered Light, Light Transmission, Signal Recognition
Having already mentioned the diffuse light test, the next part of the test focuses on different light effects.
Prolonged unprotected exposure to UV radiation can cause severe eye damage. Therefore, if protective eyewear is intended to address this issue, the lenses must guarantee the prescribed UV protection, which is verified through various tests and measurements. Classifications are indicated by filter and scale numbers on the lenses.
Scattered light reduces contrast and blurs vision. Appropriate protective eyewear can mitigate this effect. To determine if a lens is suitable, it undergoes a test where a specific laser beam passes through the lens at a defined angle, and a detector checks if the deviation and scattering of the light beam remain within acceptable limits.
The light transmission of the lens is measured using a spectrophotometer.
Testing signal recognition is crucial because limited perception of signal colors like red, yellow, green, and blue can pose significant risks. The degree of signal color distortion is assessed through appropriate light wavelength measurements.
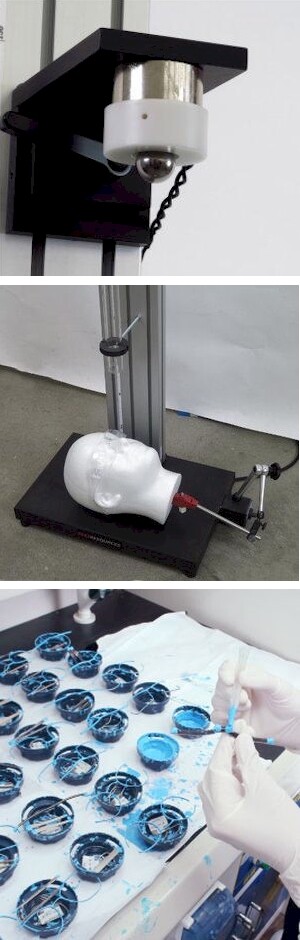
5. Field of Vision, Lateral Protection, Coverage Area
Optimal protective eyewear should not impede perfect vision or work performance. It must provide an adequate field of vision, which is evaluated through simulation tests. Additionally, the glasses should offer sufficient lateral protection and coverage to shield the eyes from side impacts.
There are several workplaces where it is particularly important for safety glasses to protect our eyes from the sides. That is why there is a frame technology that surrounds the forehead, and we can also find widened eye and side protection, thanks to which our eyes can enjoy special protection in all situations. The covering surface must meet all the criteria that are determined by the environmental factors of our workplace, so that, for example, no external impact can reach the eyes from the sides. However, this side protection must not restrict our field of vision too much.
6. Resistance to Elevated Temperatures and Aging
An important test for protection against extreme temperature exposure – marked T – is to expose the glasses to a temperature of 55°C for a full hour and then check for deformation, ageing and optical changes.
Resistance to UV ageing is also tested in some cases. This is done by exposing the lens to strong UV light for 50 hours, simulating the storage and wearing of the goggles in strong sunlight for 2 years. Various measurements are then taken to see if the goggles meet the relevant standards.
Flammability is tested by heating a steel rod to 650°C and touching it to the lens or frame. If the material does not ignite or start to glow within 5 seconds, it has passed the test.
7. Optical classification:
Depending on the degree of optical distortion, the lens of safety spectacles may be suitable for occasional wear (class 3), occasional wear (class 2) or permanent wear (class 1). In order to be classified in the best possible optical class, i.e. class 1, a pair of goggles must perform within the specified tolerance when tested against the specified correction values. This is tested using a lens gauge.
8. Material and surface quality:
Last but not least, we must also talk about the control of material and surface quality. This involves the search for and elimination of defects that could impair optical quality. This may include scratches, inclusions, bubbles or clouding.
